Insuring Workplace Well-being: The Paramount Importance of Safety Training
Safety Training Pays for its self
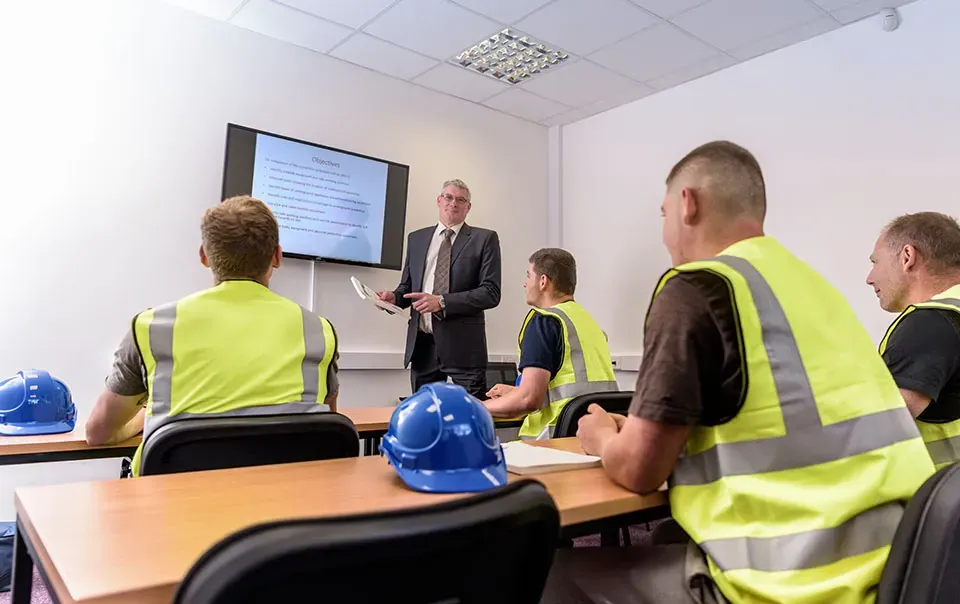
Introduction
In today's fast-paced and competitive work environment, ensuring the well-being of employees has become a fundamental priority for organizations. Workplace well-being encompasses not just physical health but also mental and emotional health, creating a holistic approach to ensuring employees can perform at their best. A critical component of workplace well-being is safety training, which is paramount in preventing accidents, reducing health risks, and fostering a culture of safety. This essay delves into the paramount importance of safety training in insuring workplace well-being, exploring its benefits, key components, and implementation strategies.
Benefits of Safety Training
1. Prevention of Accidents and Injuries
Safety training equips employees with the knowledge and skills to identify and mitigate potential hazards in the workplace. By understanding safety protocols and best practices, employees can avoid accidents and injuries, leading to a safer work environment. This prevention not only protects employees but also reduces the financial burden on organizations due to lost productivity and medical expenses.
2. Enhancement of Employee Health
Regular safety training promotes a culture of health and safety, encouraging employees to adopt safe practices both at work and in their personal lives. This proactive approach to health can lead to a reduction in work-related illnesses and stress, contributing to overall employee well-being.
3. Legal and Regulatory Compliance
Adhering to safety regulations and standards is a legal obligation for employers. Safety training ensures that organizations comply with occupational health and safety laws, avoiding legal penalties and enhancing their reputation as responsible employers.
4. Boosting Employee Morale and Productivity
Employees who feel safe and valued are more likely to be motivated and productive. Safety training demonstrates an organization's commitment to its workforce, leading to increased job satisfaction, loyalty, and morale.
5. Reduction in Workplace Absenteeism
Effective safety training minimizes the risk of accidents and health issues, leading to fewer absences. Lower absenteeism rates mean consistent productivity and reduced operational disruptions.
Key Components of Effective Safety Training
1. Comprehensive Risk Assessment
Identifying potential hazards specific to the workplace is the first step in developing an effective safety training program. A thorough risk assessment helps tailor the training to address the unique needs of the organization.
2. Engaging and Interactive Training Methods
Safety training should be engaging and interactive to ensure employees retain the information. Utilizing a mix of instructional methods, such as hands-on demonstrations, simulations, and e-learning modules, can enhance understanding and retention.
3. Continuous Improvement and Feedback
Safety training should not be a one-time event but an ongoing process. Regularly updating training materials, incorporating feedback from employees, and conducting refresher courses ensure that safety practices remain current and effective.
4. Clear Communication and Documentation
Clear communication of safety policies, procedures, and emergency protocols is crucial. Providing accessible documentation and resources helps employees understand and adhere to safety standards.
5. Leadership Involvement and Commitment
Leadership commitment to safety training is essential in fostering a culture of safety. When leaders prioritize safety and participate in training, it sets a positive example and encourages employees to follow suit.
Implementation Strategies for Safety Training
1. Tailoring Training to Specific Roles
Different roles within an organization have varying safety requirements. Tailoring training programs to address the specific risks and responsibilities of each role ensures that employees receive relevant and applicable information.
2. Utilizing Technology and Innovation
Leveraging technology, such as virtual reality (VR) simulations and mobile training apps, can make safety training more accessible and engaging. Innovative tools provide immersive learning experiences that enhance understanding and retention.
3. Encouraging a Safety-First Culture
Creating a culture where safety is a shared responsibility involves engaging employees at all levels. Encouraging open communication, reporting of hazards, and active participation in safety initiatives fosters a collaborative approach to workplace well-being.
4. Measuring and Evaluating Training Effectiveness
Regularly measuring and evaluating the effectiveness of safety training programs is crucial. Utilizing metrics such as incident rates, employee feedback, and safety audits helps identify areas for improvement and ensures continuous enhancement of the training.
Conclusion
Insuring workplace well-being through safety training is a paramount responsibility for organizations. The benefits of effective safety training extend beyond preventing accidents and injuries, encompassing improved employee health, legal compliance, enhanced morale, and increased productivity. By implementing comprehensive and engaging safety training programs, organizations can create a safer, healthier, and more productive work environment, ultimately contributing to the overall well-being of their workforce.